
Material Competence@Model.HeadlineTag.Tag>
Sealing Material Competence for the Food & Beverage Industry
Material Know-how as a Core Competency
With its special requirements for hygiene and process reliability, the food and beverage industry needs a sealing expert with extensive market know-how and expertise in materials.
Freudenberg Sealing Technologies provides specially developed materials that have all required certifications and meet global compliance requirements – US-American, European or Chinese.
Besides resistance to extreme temperatures, sealing materials need to withstand pressures and aggressive media, such as cleaning agents, fat and flavored syrup.
Material Portfolio
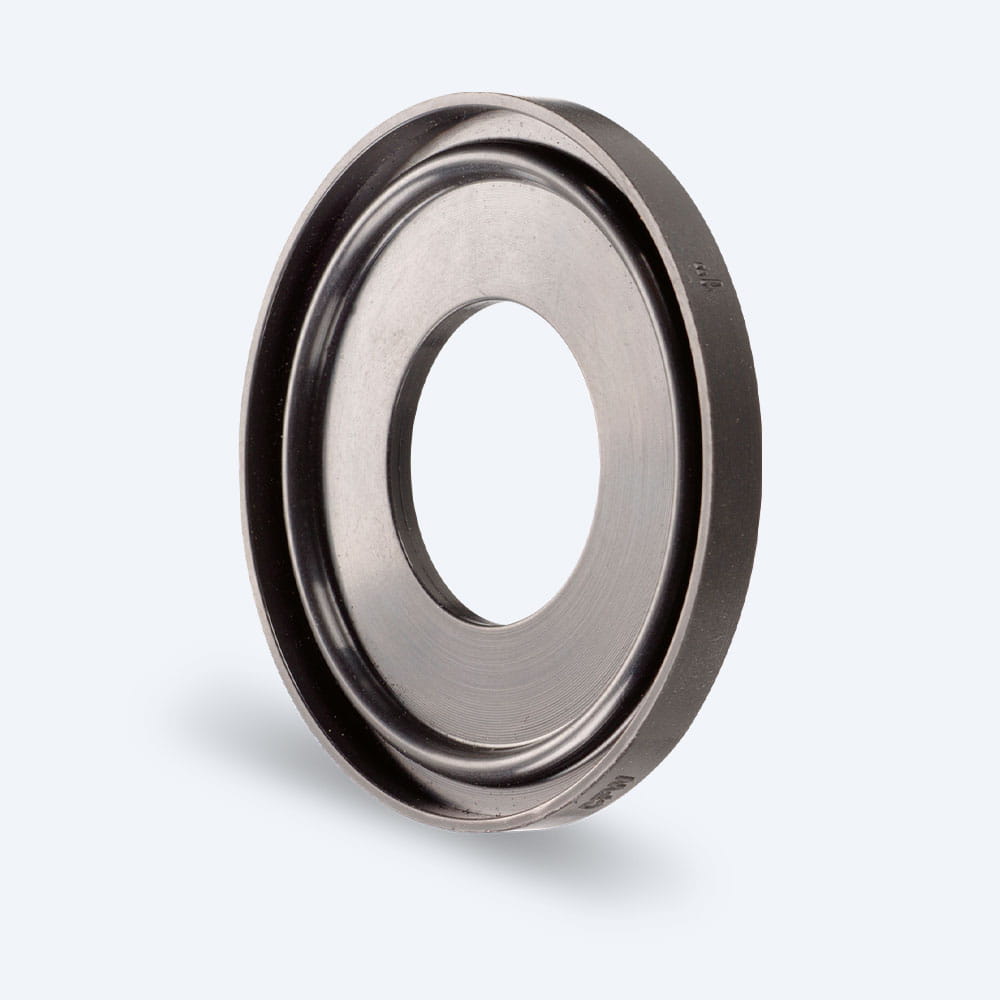
EPDM
EPDM (ethylene propylene diene rubber) is one of the most-used sealing materials in the food and beverage industry. Seals made of EPDM can be used for CIP/SIP cleaning processes, as well as for applications containing acids, lyes, polar organic solvents, alkaline solutions, water and steam (on a sustained basis up to +180 °C).
Freudenberg Sealing Technologies has developed special materials to meet these requirements and to comply with all legal regulations and conformities, including FDA standards, EU (Reg.) 1935/2004 and USP Class VI. In addition, EPDM shows very good resistance to aging, ozone and light, as well as good tensile elongation and strength. Its temperature resistance ranges between -50 °C and +150 °C, depending on the material variant. In hot water, higher temperatures of up to +180 °C are possible.
In contact with fats, flavors and oils, EPDM reaches its limit. For these applications, the universal material Fluoroprene® XP is the best choice.
Product Examples
-
O-rings made of 60 EPDM 290, 70 EPDM 291, 85 EPDM 292, 75 EPDM 386, 85 EPDM 387, 60 EPDM 334, 70 EPDM 335 and 70 EPDM 335DW
-
Customer-specific parts made of 70 EPDM 291, 85 EPDM 292, 70 EPDM 335, 85 EPDM 302 and 70 EPDM 382
-
Butterfly valve seals made of 75 EPDM 253356
-
Clamp seals made of 70 EPDM 291 and 70 EPDM 253815
-
Diaphragms made of 60 EPDM 290, 70 EPDM 291, 60 EPDM 217952 and 70 EPDM 217937
-
Elastomer bead of the Hygienic Usit® made of 70 EPDM 291 and 70 EPDM 253815
-
Profiles and cords made of 70 EPDM 391 and 80 EPDM 472
-
Machined parts made of 70 EPDM 291, 85 EPDM 292, 75 EPDM 386 and 85 EPDM 387
Try our resistance guides to check the chemical and CIP/SIP resistance of our materials.
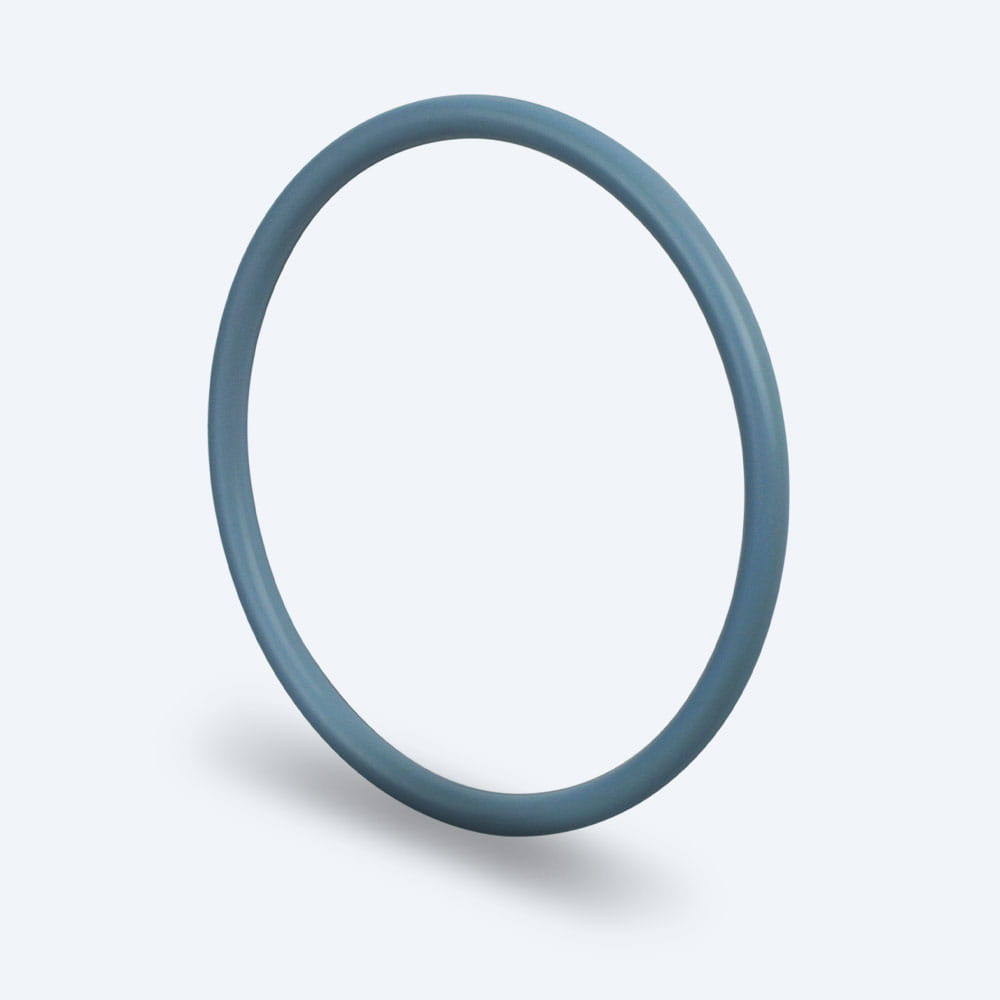
Fluoroprene XP
The universal material Fluoroprene XP is a special development of Freudenberg Sealing Technologies, perfectly adjusted to the requirements of the food and beverage industry. By unifying most of the positive characteristics of other elastomers, Fluoroprene XP is very cost-effective. Its blue color is specific to the food industry.
Fluoroprene XP displays excellent resistance in steam, hot water and numerous alkaline solutions, mineral oils, fats and acids. It is perfectly suited for CIP/SIP cleaning processes, as well as for contact with nonpolar media. It is also suitable for contact with animal and vegetable fat, which makes it an excellent candidate for the dairy industry. The material can cover a temperature range of -15 °C to +200 °C. All Fluoroprene XP material types comply with FDA standards and EU (Reg.) 1935/2004. Depending on the material type, other approvals like USP Class VI and NSF 51 are also possible. Fluoroprene XP is a perfect material for preventing flavor transfer. This can occur during product changeovers. If the material is not well suited, it will absorb flavors from the first batch and transfer it to the next.
Product Examples:
-
O-rings made of 75 Fluoroprene XP 40 and 75 Fluoroprene XP 41
-
Customer-specific parts made of 75 Fluoroprene XP 41 and 85 Fluoroprene XP 43
-
Diaphragms made of 75 Fluoroprene XP 40 and 75 Fluoroprene XP 41
-
Clamp seals made of 75 Fluoroprene XP 41
-
Elastomer bead of the Hygienic Usit® made of 75 Fluoroprene XP 45
-
Machined parts made of 75 Fluoroprene X P41 and 85 Fluoroprene XP 43
Try our resistance guides to check the chemical and CIP/SIP resistance of our materials.
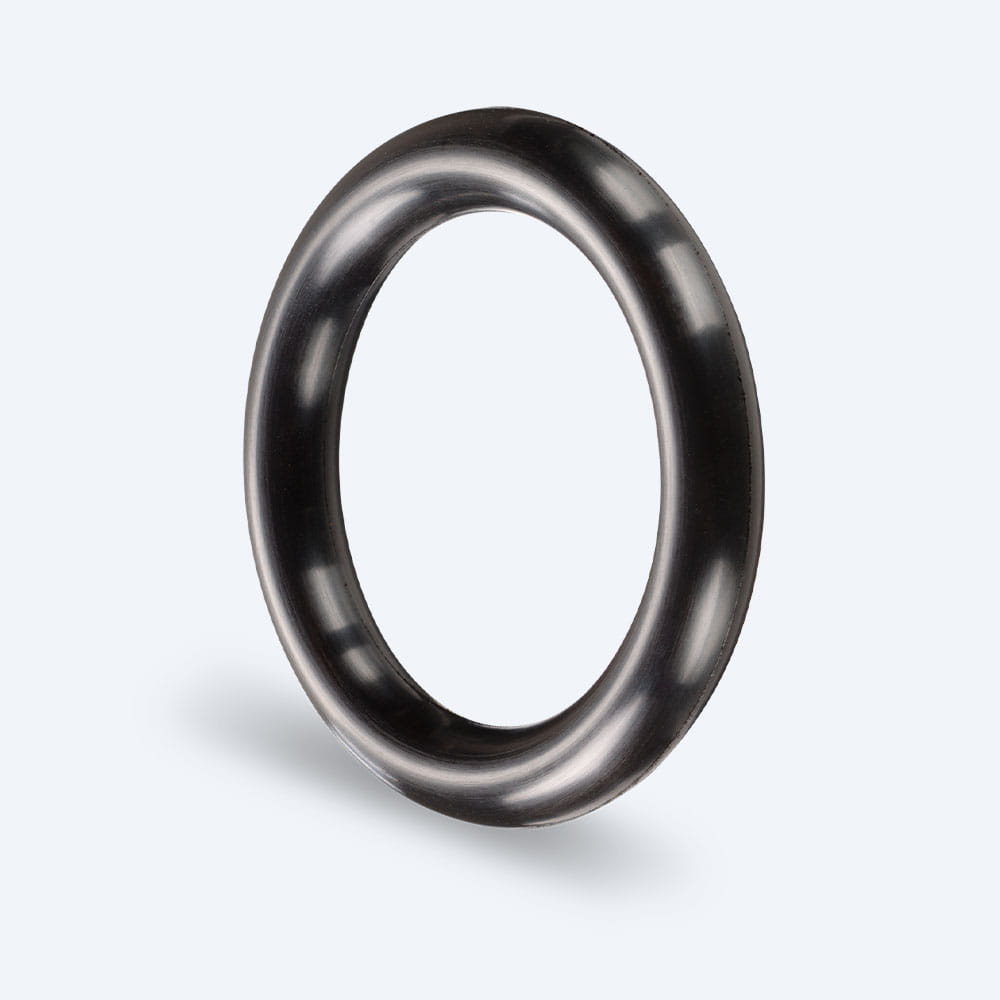
FKM
FKM (fluororubber) is a high-quality material used throughout the process industry. In the food industry, for instance, FKM is chosen when high operating temperatures are prevalent or media are used that would attack other elastomers, such as EPDM or HNBR. FKM is recommended in the beverage industry for contact with pure citrus juices, dairy products and for use in flavor oils (e.g. orange and hop oils). Our new material 75 FKM 239961 is a peroxide-cured fluororubber, which thus meets the latest regulatory requirements for food contact materials and performs well thanks to its purity and very good media resistance. It is also suitable for applications with very high operating temperatures, as the temperature range is from -25 °C to +200 °C. Currently, O-rings can be manufactured from this material. Customer-specific parts will also be possible in the future. In addition, the material is FDA-compliant and meets the requirements of EU (Reg.) 1935/2004.
Product Examples:
-
O-rings made of 75 FKM 239961
Try our resistance guides to check the chemical and CIP/SIP resistance of our materials.
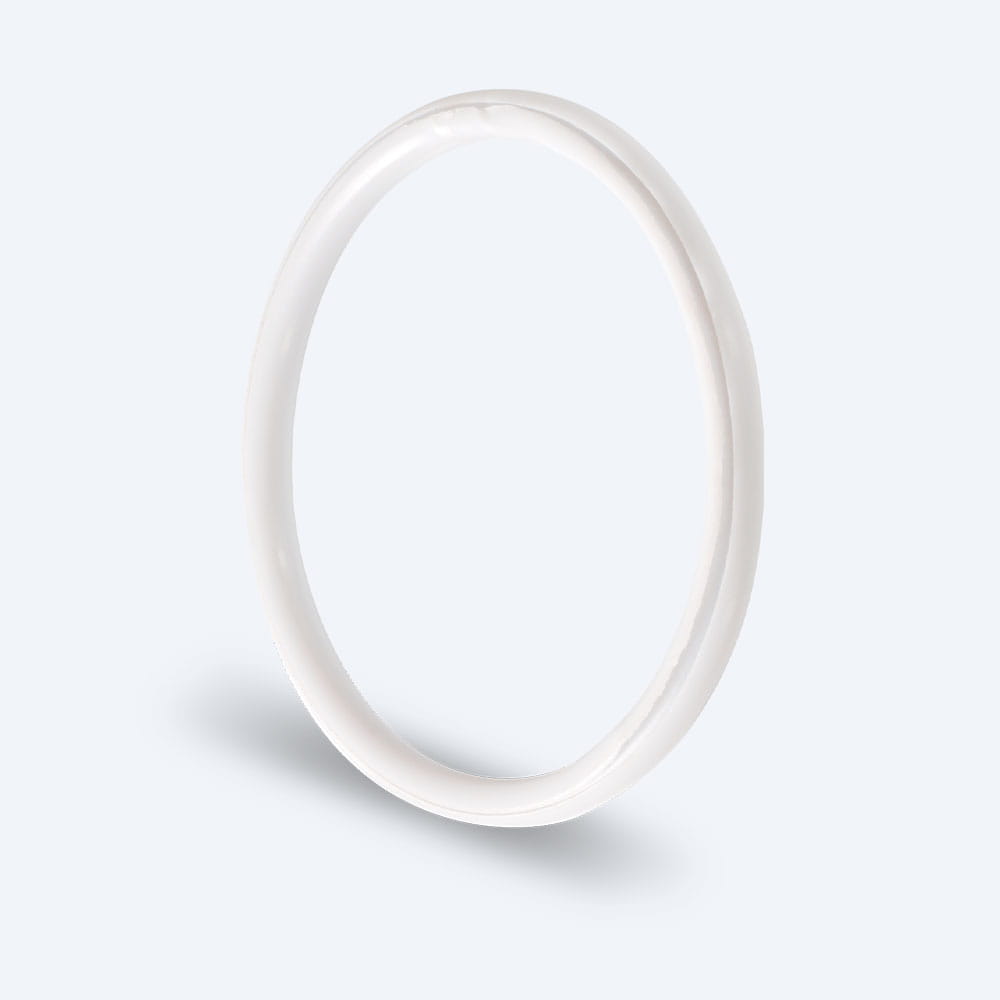
FFKM-SIMRIZ®
Simriz® perfluorelastomers (FFKM) are high-end materials for the food and beverage industry, offering the highest degree of fluorination. Freudenberg Sealing Technologies offers specially developed Simriz® materials, which comply with various legal regulations such as FDA standards and USP Class VI.
Simriz® is the material of choice when other elastomers like EPDM and FKM (including high-fluorinated types) reach their limits in extremely demanding applications. This includes very high temperatures and very aggressive media. It is suitable for use in polar and nonpolar media, allowing high concentrations and temperatures. The material is resistant to concentrated acids, amines, ketones, alkaline solutions, organic solvents, flavor concentrates and temperatures ranging between -10 °C and +325 °C, depending on the material type. In addition, the material is resistant to CIP/SIP cleaning processes and media.
Product Examples:
-
O-rings made of 75 Simriz® 494 or white 75 Simriz® 38581
-
Diaphragms made of 75 Simriz® 484
Try our resistance guides to check the chemical and CIP/SIP resistance of our materials.
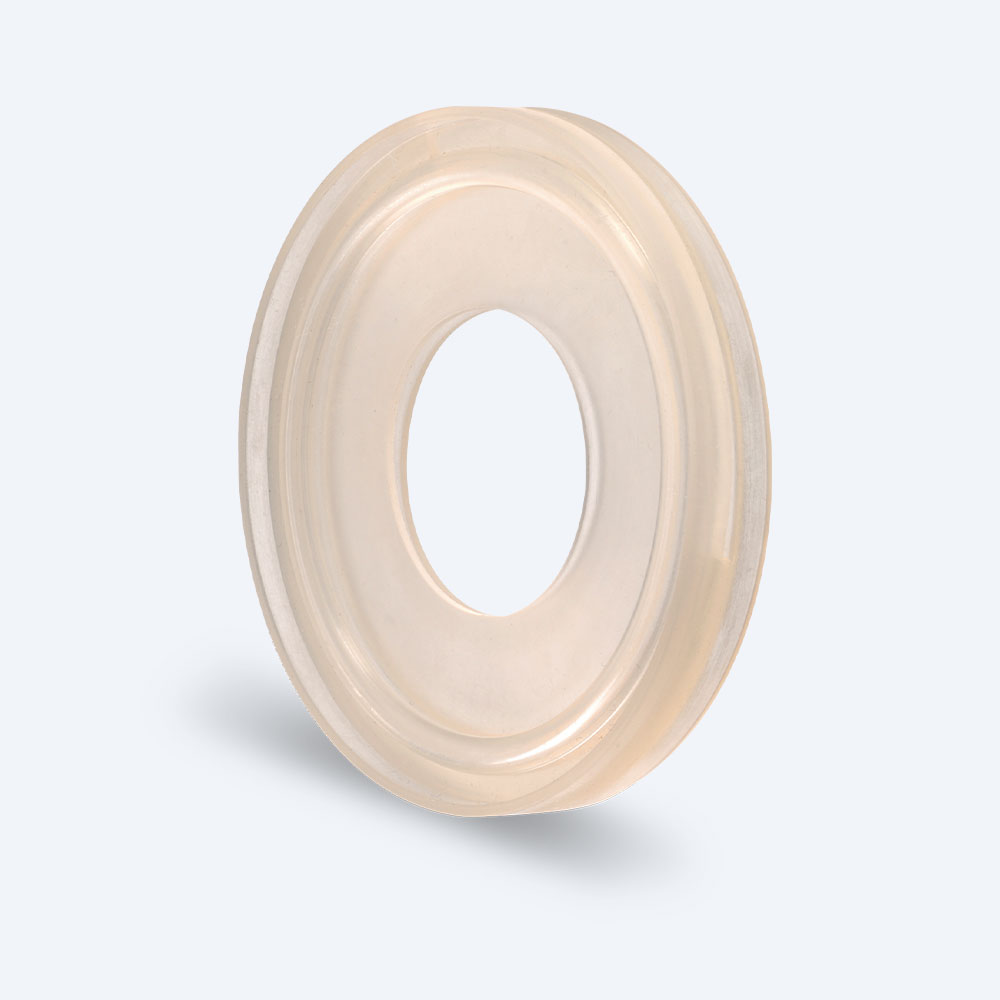
VMQ
VMQ (silicone rubber) is a synthetic polymer that is considered to be especially pure. It demonstrates very good resistance to both heat and cold, with a temperature range between -60 °C and +200 °C. VMQ is resistant to synthetic, animal and vegetable oils, glycols and solvents, which makes it an interesting material for food and beverage applications. In addition, it displays very good physiological and dielectric properties and resistance to weathering, aging and ozone.
VMQ is well suited for CIP/SIP processes excluding steam sterilization. It cannot be used in contact with concentrated acids, like nitric and formic acids, as well as in water or steam above +100 °C, esters, ethers and aromatic hydrocarbons.
Product Examples:
-
O-rings made of 70 VMQ 117055 and 78 VMQ 166898
-
Customer-specific parts made of 70 VMQ 117055, 76 VMQ 176643 and 60 VMQ 117117
-
Butterfly valve seals made of 70 VMQ 117055 and 76 VMQ 176643
-
Diaphragms made of 70 VMQ 117055 and 60 VMQ 117117
-
Clamp seals made of 70 VMQ 117055
Try our resistance guides to check the chemical and CIP/SIP resistance of our materials.
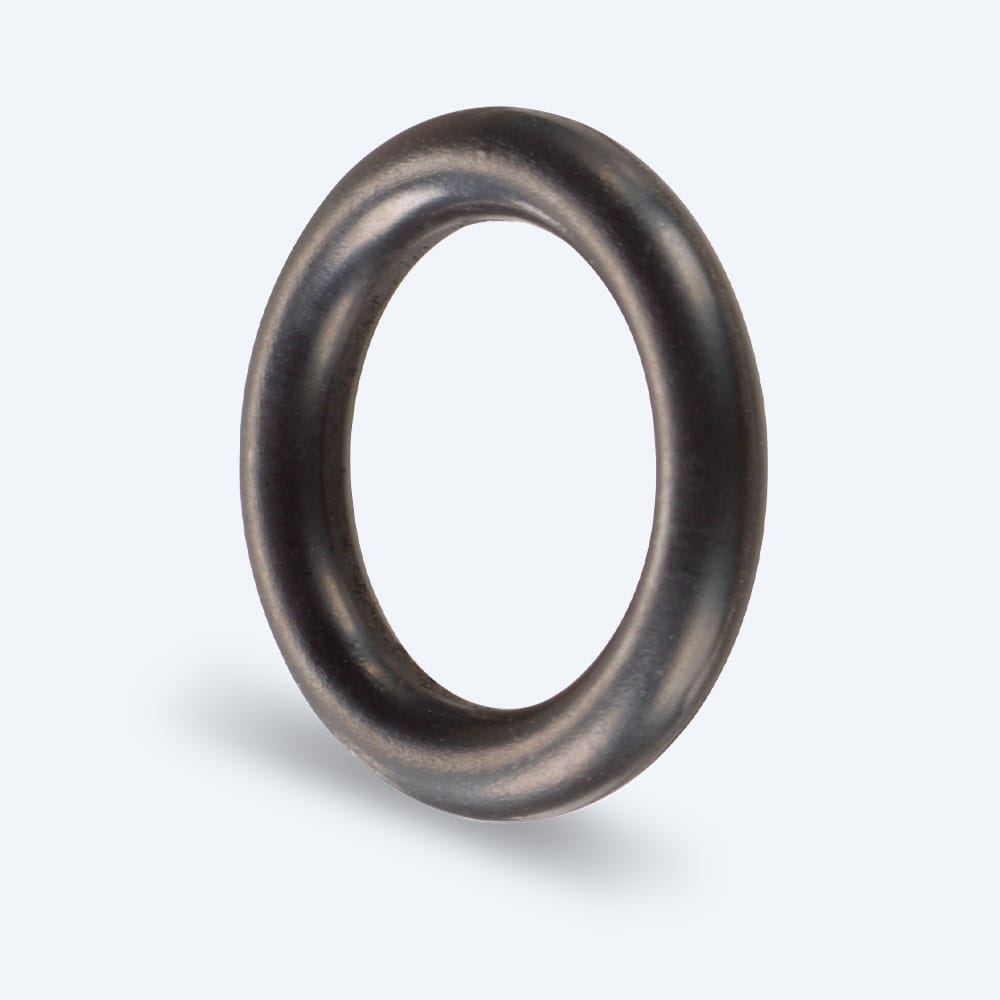
NBR
NBR (acrylonitrile butadiene rubber) is produced by polymerization of butadiene and acrylonitrile (ACN). By varying the portion of ACN, the NBR material variant will show different properties.
NBR is mainly used in applications with strong mechanical forces. Its good abrasion resistance behavior gives it a long service life. In addition, the material shows excellent resistance to vegetable and animal oils, silicones, diluted acids and alkaline solutions, depending on the temperature conditions.
NBR is unsuitable for contact with concentrated acids like nitric and formic acids, and oxidizing media like peracetic acid. The temperature resistance ranges from -30 °C to +100 °C, while special variants can be used down to -55 °C.
All NBR materials from Freudenberg Sealing Technologies for the food and beverage industry are compliant with FDA standards and the EU (Reg.) 1935/2004.
Product Examples:
-
O-rings made of 75 NBR 430 and 90 NBR 433
-
Customer-specific parts made of 70 NBR 438 and 85 NBR 436
-
Machined parts made of 70 NBR 438 and 85 NBR 436
Try our resistance guides to check the chemical and CIP/SIP resistance of our materials.
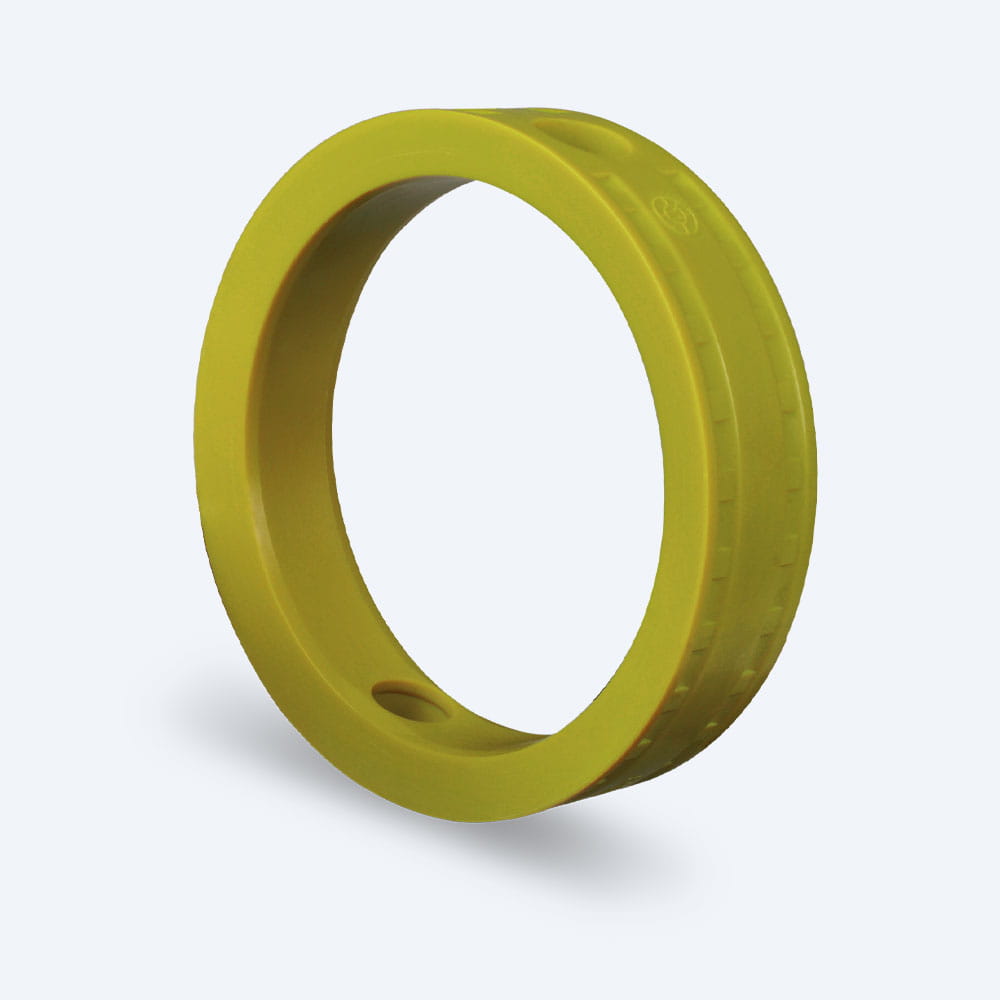
HNBR
HNBR (hydrogenated acrylonitrile butadiene rubber) offers improved heat resistance and oxidation stability. In addition, it shows high mechanical strength and improved resistance to abrasion.
HNBR is the material of choice for the dairy industry when mechanically demanding processes with abrasive products, animal and vegetable fats rule out other materials. Oils and waxes can be sealed properly with HNBR as well. As it is resistant to essential oils, such as occur in hops.
HNBR is a preferred material for breweries, where the hop is a challenge for other elastomers. It displays good performance in water and steam. The temperature resistance ranges from -30 °C up to +150 °C, depending on the material variant. HNBR is also resistant to CIP/SIP media. However, HNBR is not suitable for contact with concentrated acids, like nitric and formic acids and concentrated oxidizing media, like peracetic acid.
All HNBR materials from Freudenberg Sealing Technologies conform to FDA standards and some fulfill the requirements of the EU (Reg.) 1935/2004.
Product Examples:
-
O-rings made of 75 HNBR 231142
-
Customer-specific parts made of 70 HNBR 254067 and 85 HNBR 216553
-
Butterfly valve seals made of 70 HNBR 254067
-
Diaphragms made of 75 HNBR 181070
Try our resistance guides to check the chemical and CIP/SIP resistance of our materials.
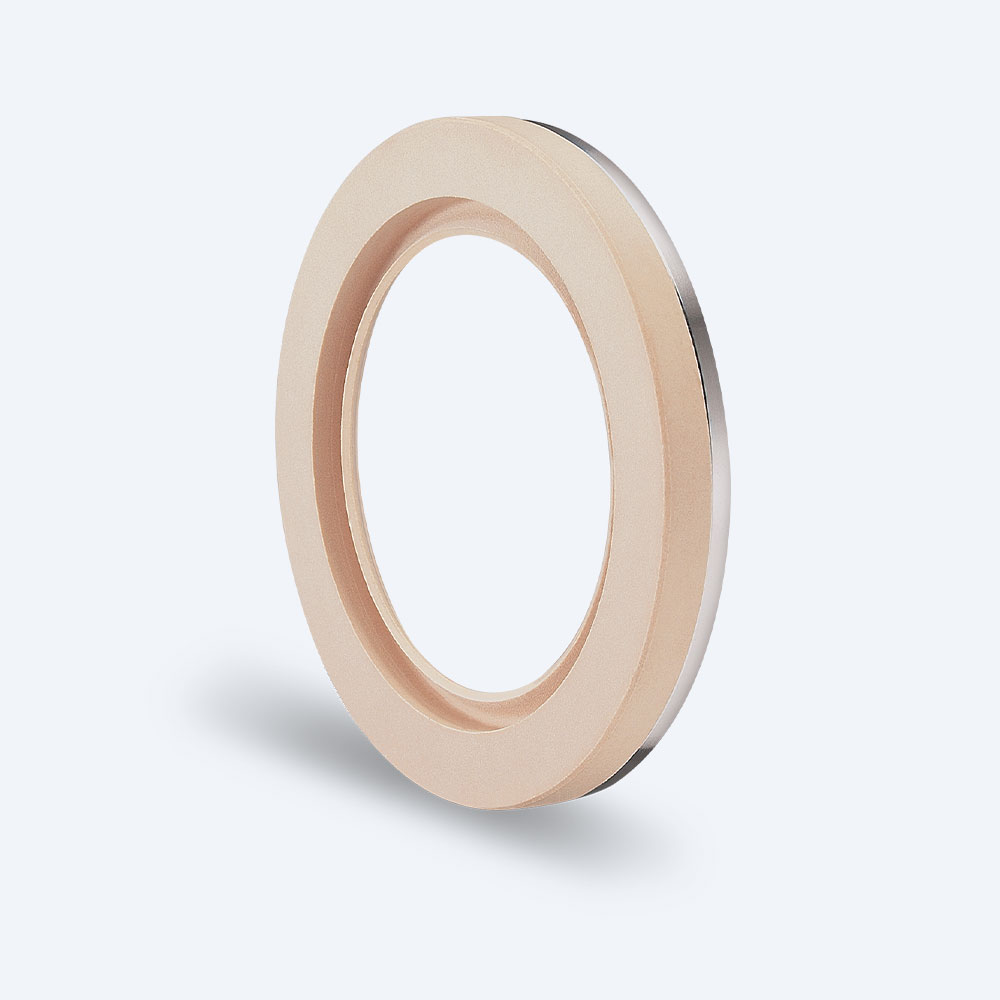
PTFE
PTFE (polytetrafluoroethylene) is a very common material in the food and beverage industry, as it displays the broadest chemical resistance of all elastomers and technical plastics and an extremely large thermal range (-200 °C to +250 °C), meaning that it can be used almost universally if no elastic behavior is required. Adding fillers can further improve specific properties such as wear resistance, electrical properties or thermal conductivity.
PTFE is resistant to acids, bases, alcohols, ketones, benzines, oils and many other substances, which demonstrates its flexibility. It only reaches its limit in contact with very strong reducing agents, such as solutions of alkali metals, or strong oxidizing agents like elemental fluorine.
PTFE glides very smoothly, meaning that it has a very low coefficient of friction and prevents what is known as the “stick-slip-effect”. In addition, its surface tension is very low, meaning that other materials hardly adhere to PTFE.
Freudenberg Sealing Technologies offers numerous special PTFE variants, which are compliant to FDA standards and EU (Reg.) 10/2011.
Product Examples:
-
Rotary shaft seals (like for example Radiamtaic® HTS II)
-
Slide bearings
Try our resistance guides to check the chemical and CIP/SIP resistance of our materials.
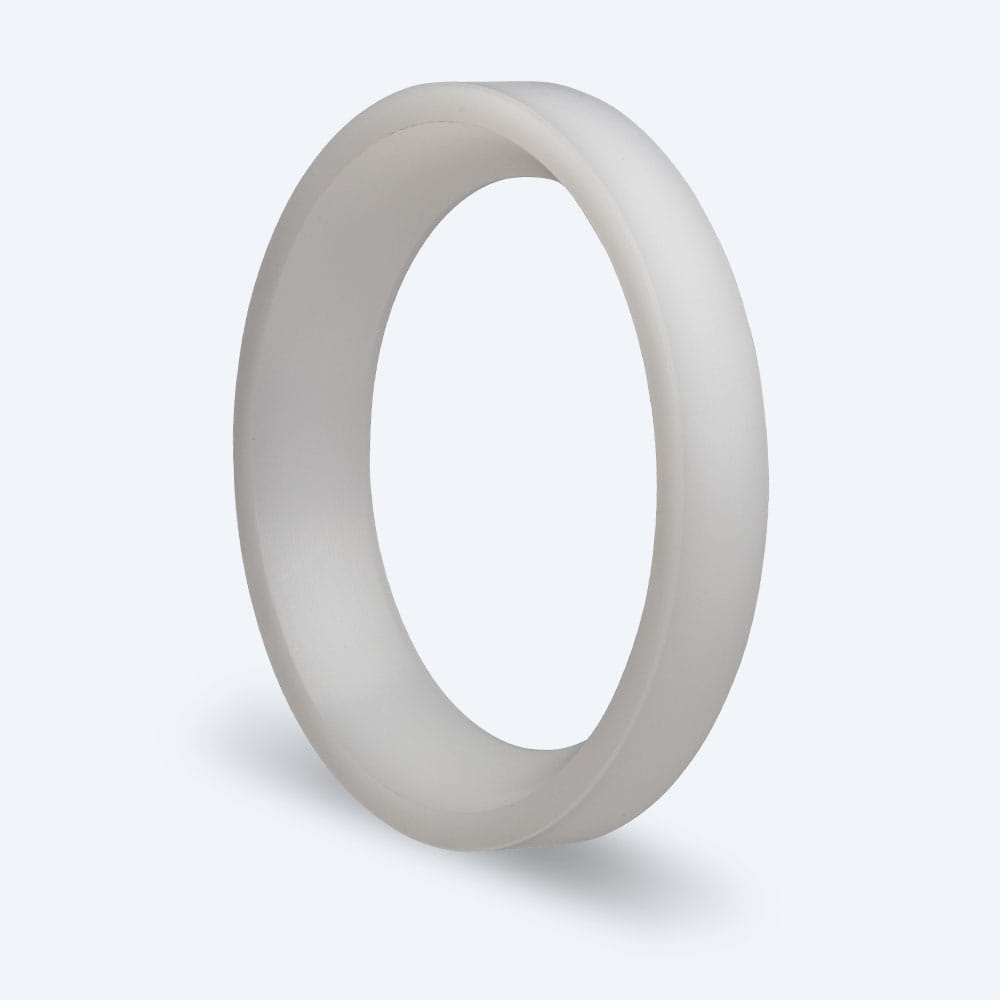
POM
POM (polyoxymethylene), also known as “polyacetal” and explored by Hermann Staudinger, is a semi-crystalline thermoplastic. It exhibits low friction, strong rigidity and abrasion resistance, as well as outstanding dimensional stability.
As a technical plastic, POM is a very stiff material – even at low temperatures down to -40 °C. The color of POM can be designed flexibly. Its water absorption is only about 0.2 %. These properties result in very stable characteristics of the seals made of POM. Beyond the tensile yield point at about 8 % at room temperature, POM shows very good resilience, strength and a low tendency to creep under repeated stress.
Many POM materials conform to FDA and German Federal Institute for Risk Assessment (BfR) standards and are therefore suitable for use in food and beverage applications.
Product Examples:
-
Back-up rings
Try our resistance guides to check the chemical and CIP/SIP resistance of our materials.
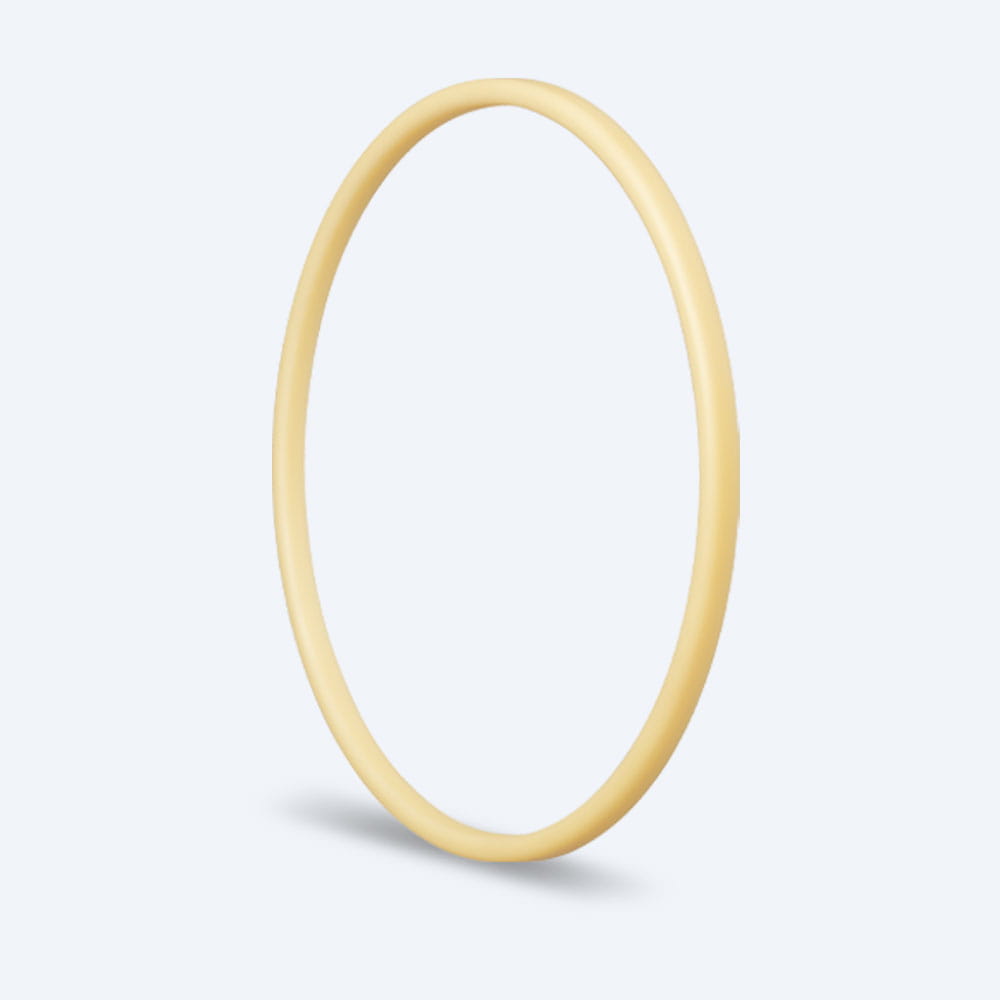
PA
Seals made of PA (Polyamide) display outstanding strength, stiffness and toughness. The material is characterized by good resistance to oil, fat, alcohol, diluted alkaline, ketones and esters, as well as good wear resistance and sliding properties. These can even be optimized by adding fiber composites with glass or carbon. As a result, PA materials can be adjusted individually to the application and its requirements.
The special variant PA12G displays low water absorption of 0.2-0.5 %. In addition, PA has hardly any tendency to creep. Its dry running features are also very good, as is its damping power.
Product Examples:
-
Back-up rings
Try our resistance guides to check the chemical and CIP/SIP resistance of our materials.
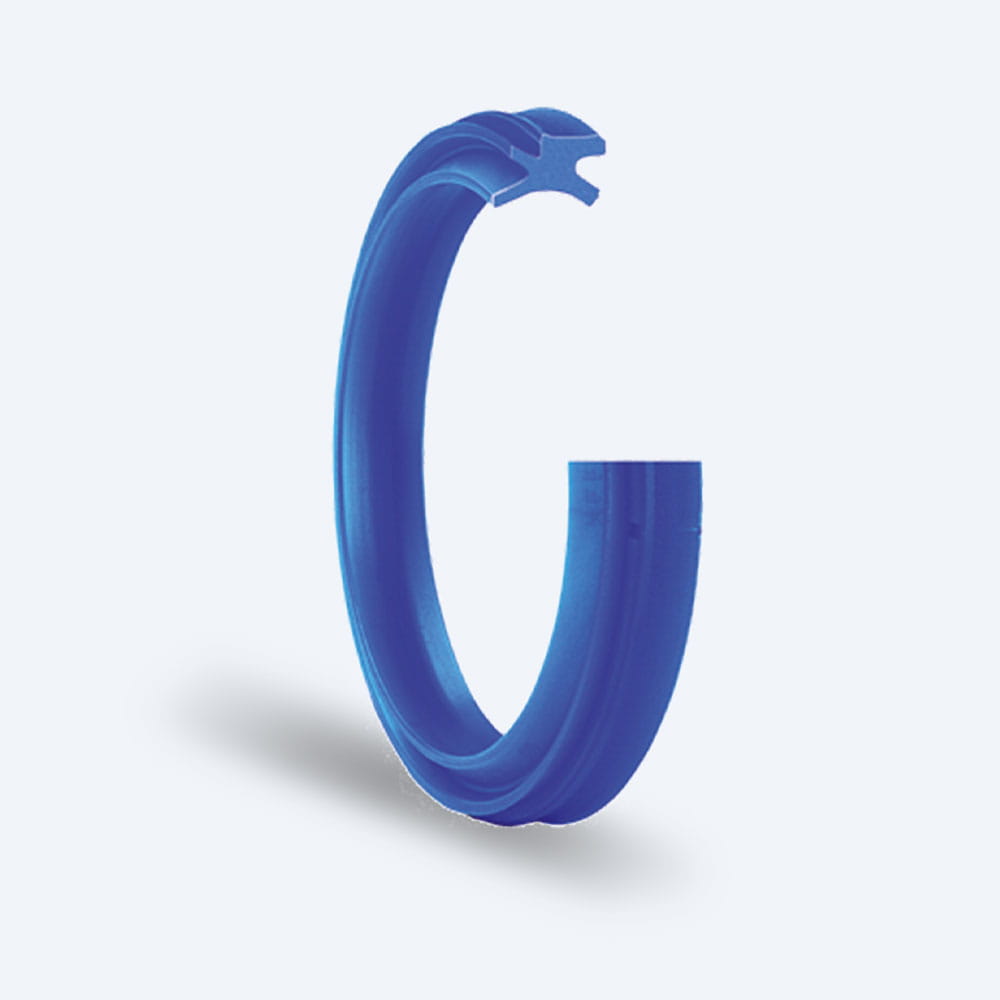
PU
PU (polyurethane), also known as “PUR”, is a very flexible polymer in terms of production methods, which makes it possible to vary properties like chemical behavior over a broad range.
Freudenberg Sealing Technologies offers specially developed high-performance PU materials such as 94 AU 21730 or 93 AU V167, which are also suitable for machining technology. These materials are compliant with FDA standards and the EU (Reg.) 10/2011.
PU materials are durable and have a high elongation at break combined with outstanding tensile strength for an elastic material. Its elasticity also sets this material apart from other plastics. In addition, PU is highly resistant to wear, oil and ozone. It is unsuitable for contact with amines, glycols and chlorinated solvents.
Product Examples:
Try our resistance guides to check the chemical and CIP/SIP resistance of our materials.
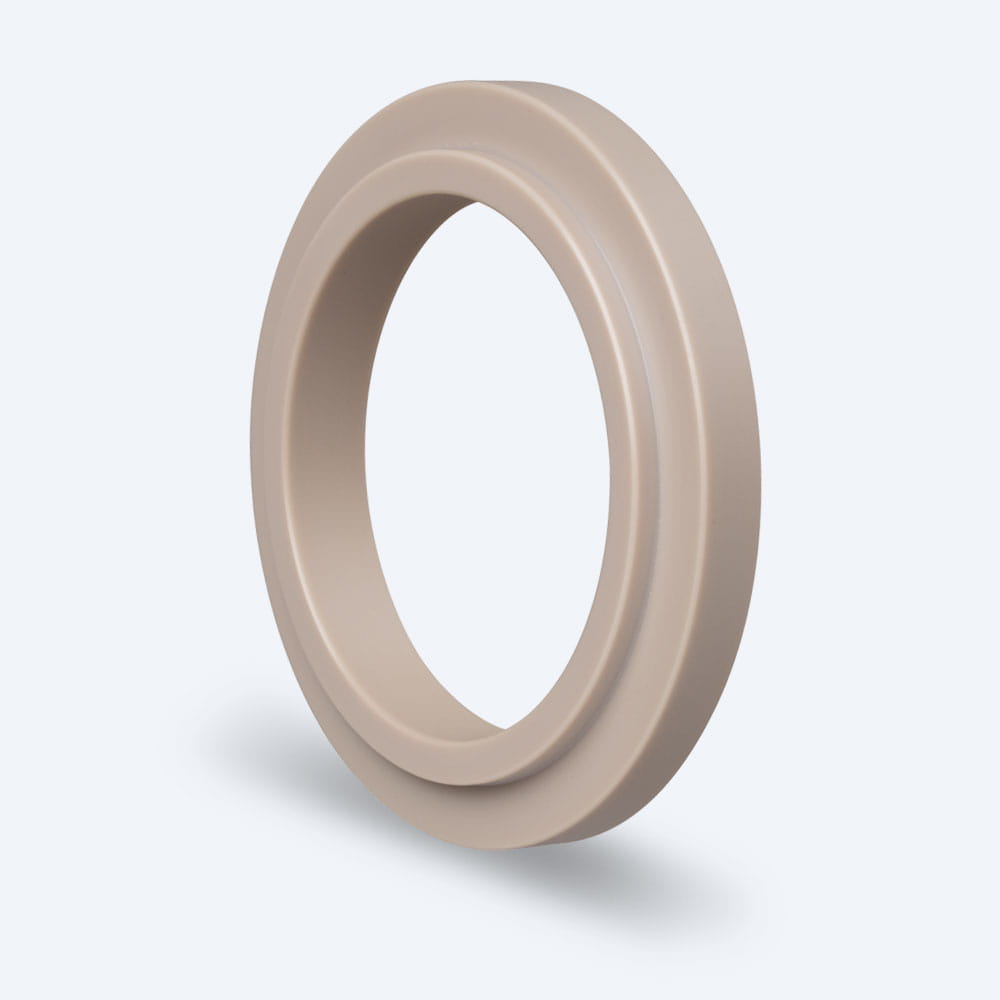
PEEK
The chemical resistance of PEEK (polyether ether ketone) materials is quite similar to that of PTFE materials. However, the mechanical properties of PEEK are superior. It is known to be almost universally media and pressure resistant. In addition, it is used for applications involving very high temperatures (up to +260 °C in long-term operations) and offers high wear resistance and electrical and thermic isolation.
When PEEK is used in unfilled versions, FDA compliance for food and beverage applications is given. Optional fillers like glass or carbon fibers can further improve the mechanical properties.
Product Examples:
-
Back-up rings for O-rings
-
Back-up rings in V-seal set packings
-
Compression rings in V-seal set packings
Try our resistance guides to check the chemical and CIP/SIP resistance of our materials.
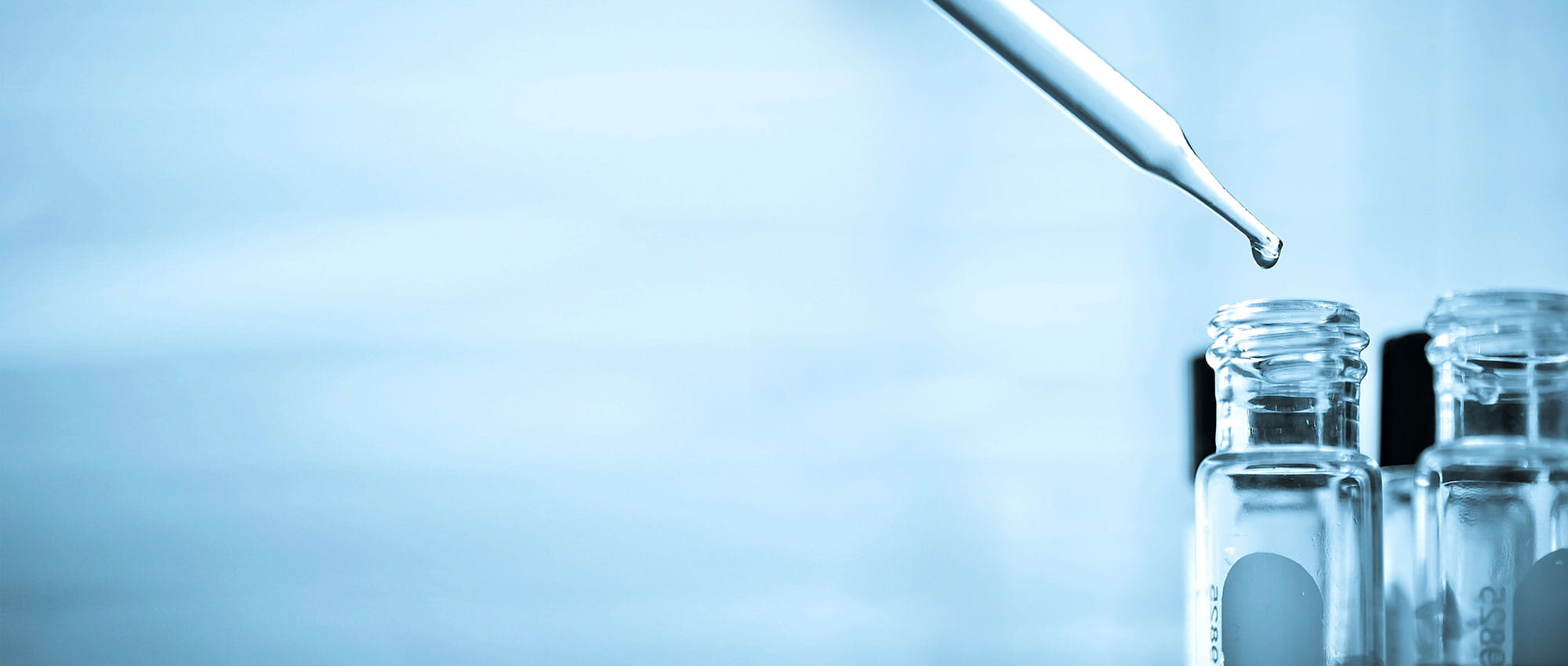
CHEMICAL RESISTANCE GUIDE
Still lost in spreadsheets?
Just a few clicks and you know which material is resistant to which process media.
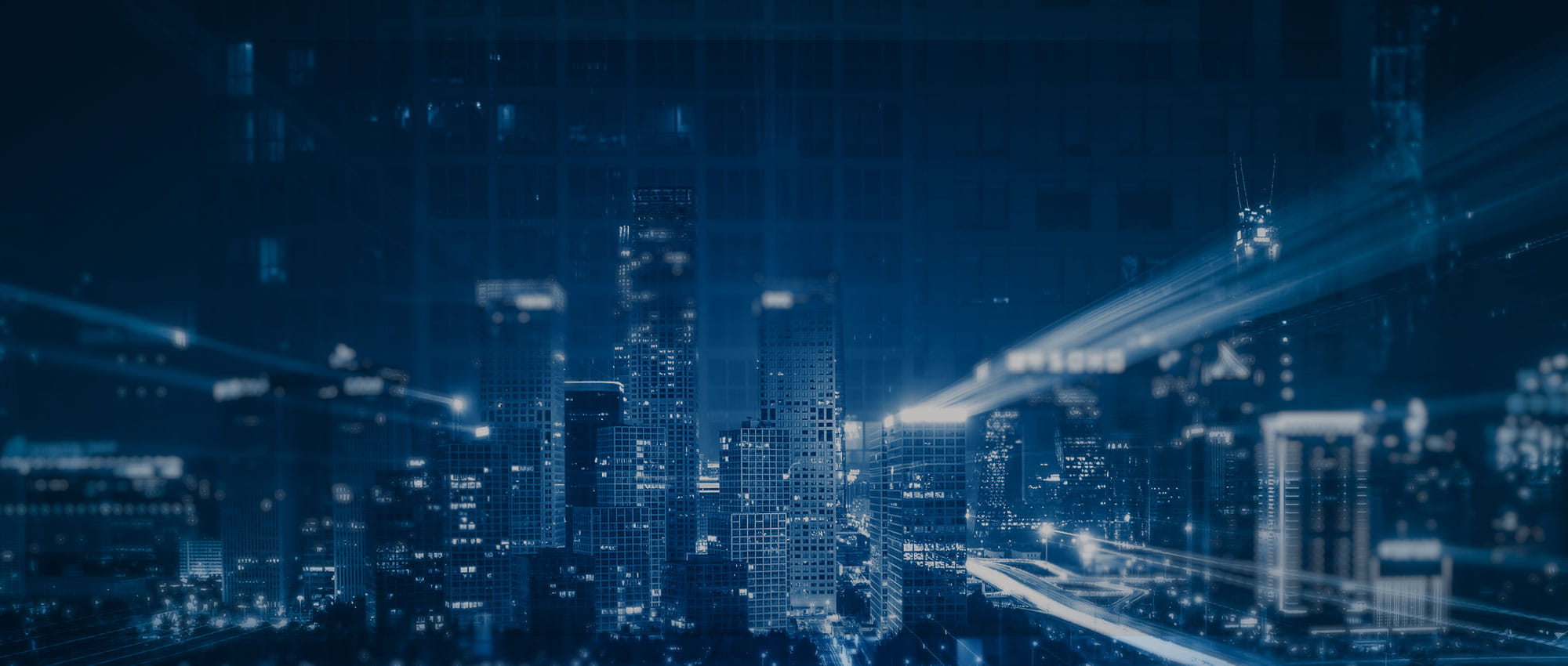
Join Us!
Experience Freudenberg Sealing Technologies, its products and service offerings in text and videos, network with colleagues and stakeholders, and make valuable business contacts.
Connect on LinkedIn! open_in_new