
EHEDG-Approval for Tubular Heat Exchanger@Model.HeadlineTag.Tag>
EHEDG-Approval for Tubular Heat Exchanger
As a technology leader, Freudenberg Sealing Technologies is the specialist for innovative sealing solutions in the process industry. Our focus is on innovation and partnership. Together with our customers, we develop tailor-made materials and sealing products according to segment- or customer-specific requirements, such as approvals, Hygienic Design and CIP/SIP processes.
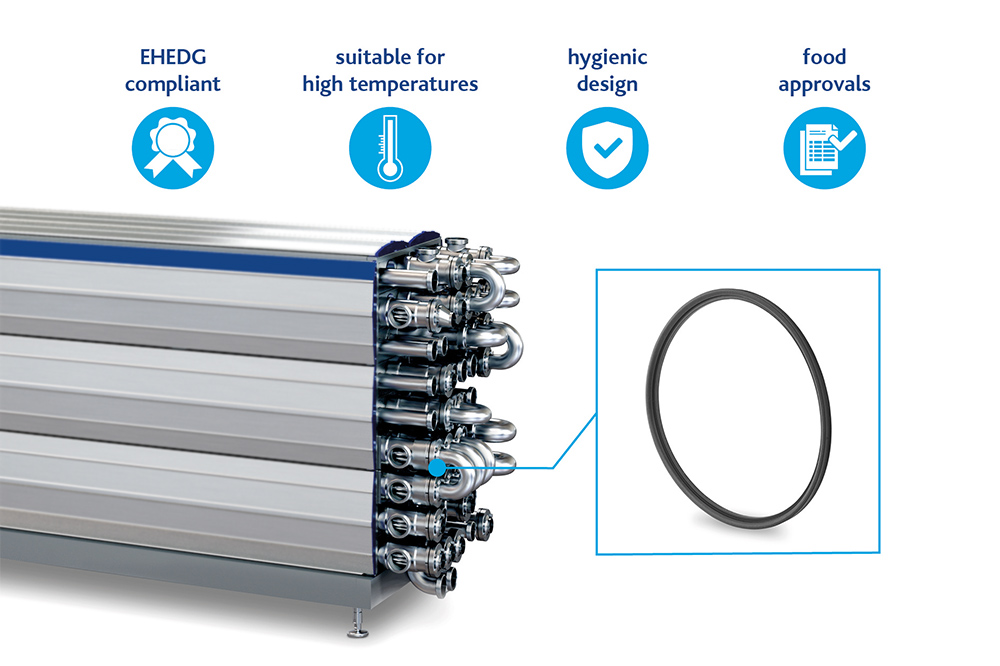
Benefits at a Glance
-
First and only tubular heat exchanger with EHEDG-approval on the market (based on the recent EHEDG guidelines)
-
Sealing materials offer compliance with the relevant legal regulations, withstand high temperatures and are suitable for CIP/SIP cleaning processes
-
Sealing design complies with hygienic design standards and offers a long operating lifetime
-
Cost-effective sealing solution
-
Reduced sampling costs due to prototyping with Freudenberg Xpress® and in-house FEM-calculations
-
Continuous expert consultation and long-standing experience as part of the Freudenberg Group
The Customer
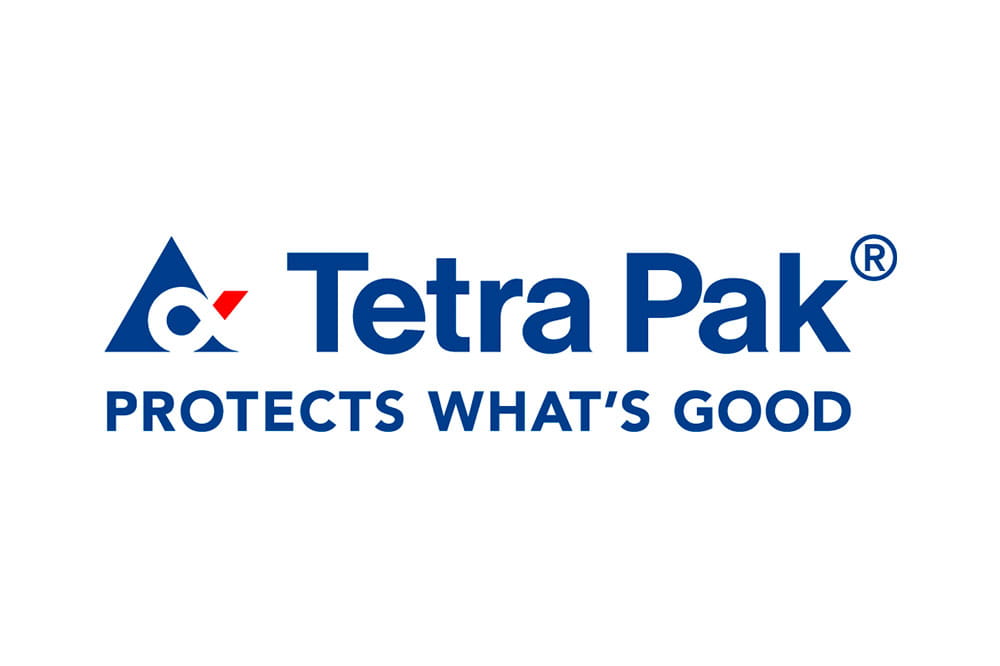
As one of the three companies in the Tetra Laval Group, Tetra Pak develops and produces innovative processing and packaging equipment for foods and beverages – from liquid food products to ice cream, vegetables or even pet food.
Segment & Application
Our customer Tetra Pak focuses on the development of safe and hygienic processing and packaging for foods and beverages and emphasizes close cooperation with its customers and development partners. The supply of complete systems for processing, packaging and distribution not only protects foods and beverages and their taste, but also prevents them from being wasted and minimizes the use of resources.
Development & Solution
Tetra Pak needed a cost-effective hygienic seal that connects the stainless steel parts of its newly developed tubular heat exchanger and is therefore a very important part of the application. The requirements are challenging: Compliance with the hygienic design standards of the EHEDG (European Hygienic Engineering and Design Group) as well as with industry-specific legal regulations, such as FDA, EG (Reg.) 1935/2004 and 3-A Sanitary Standards are essential in order to prevent contamination in the product path and enable a direct product contact. At the same time the sealing material needs to withstand a wide temperature range. Additionally, the design should be optimized for cleaning in CIP/SIP processes and offer a long operating lifetime.
Due to a very good impression of Freudenberg‘s research, development and production capabilities as well as good experience with partnership developments for homogenizers in the past, Tetra Pak decided to go with Freudenberg Sealing Technologies for this development project. The possibility to order machined prototypes from Freudenberg Xpress® as well as the advantages of Freudenberg‘s latest EPDM generation that is suitable for injection molding convinced the customer even more. In very close cooperation with the technical team at Tetra Pak Processing Equipment the experts at Freudenberg Sealing Technologies started to develop a product seal with optimized design and better performance according to Tetra Pak‘s requirements for use in the new tubular heat exchanger.
Thanks to the digital modelling possibilities (FEM) at Freudenberg‘s technology center the lifetime behavior of the seal and its material could already be predicted in the beginning. Suitable prototypes were machined with the Freudenberg Xpress® service, which saved time and costs because no tooling production was necessary. The continuous close collaboration between the different departments and with the customer helped to overcome various challenges during the development phase, such as the high temperatures that were very complex to handle in the FEM analysis. In the end all requirements could be fulfilled and the whole application received EHEDG-approval.
Both sealing materials, 70 EPDM 291 and 75 Fluoroprene XP 40, proved to offer a very good performance in CIP/SIP cleaning media. Additionally, they comply with the legal requirements of the FDA, EG (Reg.) 1935/2004, NSF 51 as well as 3-A Sanitary Standards. The temperature range of 70 EPDM 291 is between -40 °C to +150 °C, while 75 Fluoroprene XP 40 stands up to temperatures of -15 °C to +200 °C.
The first size of the product seal is already approved and is running in series. Four more dimensions will follow.
Do You Already Know Our Other Success Stories?